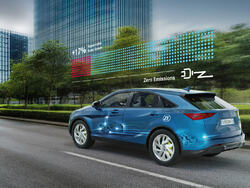
La visione di ZF per il futuro dell’automotive si traduce in un percorso che punta alla neutralità climatica entro il 2040, spingendo su economia circolare e digitalizzazione a 360 gradi.
Componentista di primo impianto e produttore di ricambi per il settore aftermarket, ZF conosce bene tutto il mondo automotive e le sfide che deve affrontare.
Nel corso di un incontro stampa online, un appuntamento oramai tradizionale che si trova sotto il nome di “Aftermarket chat”, l’azienda di casa madre tedesca punta i riflettori su un tema chiave, trasversale a più settori, ma declinato in ottica aftermarket: la sostenibilità.
La sostenibilità: un concetto chiave
Philippe Colpron, responsabile del settore aftermarket per ZF, entra nel dettaglio di ciò che significa questo concetto per ZF: “Naturalmente, essendo nel settore della mobilità, il miglioramento dell'impatto ambientale è insito nel nostro DNA. Attraverso l'evoluzione tecnologica dei sistemi di propulsione, dall'ICE all'ibrido e all'elettrico, con una quota crescente di tecnologie guidate dal software, il nostro ruolo è quello di accompagnare i nostri clienti nei momenti di trasformazione”.Ma la sostenibilità non è solo quella da realizzare a livello di trasporti, ma anche di efficientamento aziendale, nella produzione come nei processi.
“È nostra responsabilità – continua Colpron -, in quanto azienda manifatturiera, rivedere e adattare i nostri processi produttivi: dal consumo energetico alla gestione dei rifiuti dei nostri impianti, passando per l'economia circolare attraverso i processi di rigenerazione, ad esempio, dobbiamo ripensare costantemente il nostro modo di operare. Comprendere la complessità di questo tema significa rendersi conto che dobbiamo lavorare insieme ai nostri partner per raggiungere gli ambiziosi obiettivi del nostro settore”.
La sfida, per ZF, è arrivare a raggiungere la neutralità climatica entro il 2040, mettendo in campo tutte le risorse disponibili e attivandosi in tutti gli aspetti dove è possibile fare la differenza, per raggiungere l’obiettivo zero emissioni, ma anche zero incidenti e zero tempi di guasto del veicolo.
Per fare questo bisogna agire lungo tutta la filiera, realizzando nuove alleanze che coinvolgano tutti e permettano di condividere un nuovo approccio al mercato, che ZF definisce come mobilità di nuova generazione CASES, acronimo di Connected, Autonomous, Shared, Electrified, Sustainable (connesso, autonomo, condiviso, elettrificato, sostenibile).
In sintesi, per ZF significa essere attiva e presente con prodotti e servizi, portare avanti le necessarie trasformazioni sia al proprio interno sia verso il mercato, offrendo un supporto globale a tutti i protagonisti della filiera aftermarket.
La digitalizzazione
“Oltre alle nuove tecnologie, come le auto connesse, uno dei principali fattori trainanti per il mercato dei ricambi è la digitalizzazione” spiega Colpron. È su questo versante, infatti, che si stanno concentrando molte aziende per portare una informatizzazione spinta a tutti i livelli della filiera, allo scopo di disegnare una mobilità non solo più sostenibile, ma anche più sicura.“Le soluzioni digitali - sottolinea Colpron - non solo consentono la trasparenza nelle nostre complesse catene di approvvigionamento, ma massimizzano anche i tempi di operatività e riducono al minimo il consumo energetico. Inoltre, consentono un processo decisionale preciso e basato sui dati, la semplificazione di una complessità crescente e l'introduzione di nuovi modelli di business, il tutto per una mobilità più verde, più snella e più sicura per tutti, un fattore chiave della nostra visione Zero (che risponde agli obiettivi di zero emissioni, zero incidenti e zero downtime per ogni chilometro percorso)”.
Colpron fa poi un esempio concreto di come le soluzioni digitali possono contribuire ad efficientare tutto il sistema. “Con le nostre soluzioni digitali per le flotte, ad esempio, aiutiamo i nostri clienti a operare in modo più efficiente sfruttando l'accesso remoto ai dati dei veicoli, come le trasmissioni o gli pneumatici, e l'analisi predittiva, permettendoci di aspirare allo zero downtime. I dati analizzati digitalmente comportano una riduzione non solo dei costi (tempo di guida, carburante, manutenzione, ecc.), ma hanno anche un impatto diretto sull'impronta ecologica di una flotta”.
Non va trascurato poi l’aspetto del ricambio generazionale: le nuove leve, infatti, hanno maggior dimestichezza con queste tecnologie e pertanto sono anche più propense a utilizzarle in ambito lavorativo. Non solo, ma secondo Colpron, enfatizzare la trasformazione tecnologica permette anche di attrarre più facilmente le nuove generazioni, offrendo nuovi orizzonti per dei mestieri che hanno una lunga tradizione.
“Le nuove generazioni pensano prima di tutto al digitale: i talenti esperti di tecnologia ed eco-consapevoli sono una forza trainante per il cambiamento sostenibile. Questi talenti spesso non conoscono l'aftermarket e il suo vasto campo di attività e quindi non lo considerano un'area di sviluppo della carriera o addirittura un settore in cui possono contribuire alla mobilità del futuro. L'industria dell'aftermarket deve lavorare insieme per realizzare questo cambiamento. Per essere preparati al meglio per il futuro, dobbiamo passare a una mentalità digitale per attrarre i talenti giusti per la sostenibilità del settore aftermarket” conclude Colpron.
Stefanie Bohnet, che si occupa di risorse umane per l’area soluzioni digitali per l’aftermarket di ZF, nella sua presentazione sottolinea ancora meglio questo aspetto, spiegando che per l’azienda è un dovere imprescindibile quello di accompagnare i propri clienti nel percorso di trasformazione. Intercettare nuovi talenti e rivolgersi ai cosiddetti “nativi digitali” è un imperativo per una azienda che come ZF non solo guarda al futuro, ma rappresenta il futuro nell’automotive.
L’economia circolare
Uno degli aspetti fondamentali per ottenere risultati sicuri in termini di sostenibilità è puntare sul riciclo e riutilizzo dei materiale e dei componenti: la cosiddetta economia circolare.Tomasz Galazka, responsabile della strategia e dello sviluppo del business dedicato al remanufacturing, dichiara: "con la rigenerazione in serie dei componenti di veicoli, è possibile risparmiare fino al 90% delle materie prime utilizzate per la produzione di ricambi nuovi”. I prodotti rigenerati, come sottolinea Galazka, offrono la massima sicurezza e affidabilità, come fossero prodotti nuovi, perché vengono utilizzati gli stessi standard e sottoposti ai medesimi test dei prodotti di primo impianto, tanto che la garanzia offerta da ZF è la stessa per il nuovo e il rigenerato.
Gli elementi costitutivi della rigenerazione in ZF sono stati definiti durante lo sviluppo del prodotto. Nel suo nuovo standard "Design for Sustainability", ZF delinea i requisiti associati ai componenti che possono essere rigenerati. Questo serve da guida per un ciclo di vita del prodotto sostenibile e a basso consumo di risorse. L'obiettivo dell'azienda è che il maggior numero possibile di prodotti ZF abbia i requisiti tecnici necessari per una "seconda vita".
Tra i modi in cui ZF si sta impegnando in questo senso vi sono l'utilizzo di materiali più resistenti alla corrosione e l'impiego di tecnologie di connessione che consentano uno smontaggio senza danni. “In questo modo – spiega Galazka -, anche i componenti del veicolo che non possono ancora essere rigenerate in modo economico o fattibile confluiranno nel ciclo dei materiali. Inoltre, alcune prossime generazioni di prodotti sono già progettate in modo da poter essere rigenerate”.
Un esempio è l'iABS di ZF a marchio WABCO, la terza generazione del suo ABS (sistema antibloccaggio) per rimorchi. Tra i vari miglioramenti, il design tiene conto di un miglior accesso al circuito stampato, che ora è anche riflashabile.
Un altro progetto attualmente in fase di sviluppo è incentrato sui metodi di rigenerazione dei componenti della trasmissione elettrica e dei sensori dei sistemi di assistenza alla guida.
ZF sta preparando uno studio di fattibilità per determinare in che misura i motori elettrici, le batterie ad alta tensione, gli inverter e i sistemi di telecamere siano adatti al riutilizzo e possano essere aggiornati.
Ad oggi, l’azienda offre in totale più di 5.500 prodotti diversi (codici ricambi) che vengono rigenerati in 20 sedi ZF in tutto il mondo, dalle pinze freno ai sistemi sterzanti, fino ai cambi automatici.
ZF non vuole solo rafforzare l'impegno per l'economia circolare all'interno dell'azienda, ma crede fermamente che anche i clienti, i partner e le altre parti interessate debbano essere coinvolti in questa iniziativa.
Philippe Colpron sottolinea: "incoraggiamo i nostri clienti e partner a unirsi a noi per dare forma a un futuro più verde, partecipando attivamente alla catena del valore della rigenerazione. Per molti clienti, la sostenibilità sta diventando sempre più importante quando si tratta di riparare i veicoli. Ecco perché le officine dovrebbero offrire attivamente ricambi rigenerati e restituire i core che non siano danneggiati per dar loro una seconda vita. Perché una vera economia circolare può avere successo solo se lavoriamo tutti insieme".
Logistica e aftermarket: una alleanza green
Per chi come ZF punta a una totale sostenibilità ambientale del proprio business, la logistica è un tassello fondamentale."Il compito della nostra logistica sostenibile è quello di fornire la giusta quantità di prodotti ZF Aftermarket nel posto giusto, al momento giusto, nella giusta qualità e al giusto costo, con il minor consumo possibile di risorse e le minori emissioni possibili", spiega Everton da Silva, responsabile delle Operazioni a livello globale. "E noi incrementiamo la nostra sostenibilità attraverso la digitalizzazione della supply chain". Ecco dunque che il cerchio si chiude, con l’apporto della digitalizzazione dei processi.
A partire dagli stabilimenti, dove ad esempio si utilizzano impianti di cogenerazione autogestiti o sistemi fotovoltaici per la produzione di energia, ZF lavora per ridurre le emissioni di CO2 e gli effetti dei gas serra avvalendosi della digitalizzazione delle imprese.
Ad esempio, si punta a migliorare la trasparenza nell'approvvigionamento delle materie prime e a consentire una risposta rapida alle interruzioni della catena di fornitura. “Grazie alle simulazioni – sottolinea Everton da Silva - è possibile ridurre la necessità di trasporto aereo e, di conseguenza, le emissioni di CO2 fino al 5% circa”.
“L'utilizzo di una piattaforma di produzione digitale - spiega da Silva - riduce al minimo gli sprechi energetici. Alcuni esempi sono: la gestione dell'aria compressa, la gestione degli arresti, la riduzione delle temperature di lavaggio, la gestione automatica dei carichi, il controllo basato sulle esigenze dei sistemi tecnici dell'edificio e dei grandi consumatori come le presse e le macchine utensili, la sostituzione dei processi basati sul gas come la tempra e i sistemi avanzati per la manutenzione preventiva delle linee di produzione.
Allo stesso modo, previsioni avanzate e strumenti digitali di pianificazione delle vendite, dell'inventario e delle operations (SIOP) migliorano la qualità dell'inventario, riducono le consegne urgenti, la produzione non necessaria e lo spreco di risorse. Continuiamo a servire i prodotti in tempo secondo le aspettative dei clienti, con prodotti di qualità ma nel modo più efficiente dal punto di vista ambientale.
Prevedendo con precisione la domanda dei clienti grazie all'apprendimento automatico e all'analisi predittiva – continua da Silva -, saremo in grado di posizionare le merci più vicino ai nostri consumatori per ridurre i tempi di consegna e le emissioni di carbonio, diminuendo i chilometri percorsi e i costi operativi. La migliore disponibilità della categoria nei magazzini di ZF Aftermarket e la collaborazione nella gestione delle scorte dei clienti, ad esempio, riducono del 70% la necessità di spedizioni espresse e quindi l'impronta di CO2. Allo stesso modo, un layout di magazzino più efficiente consente di risparmiare tempo, energia, spazio e denaro, oltre a contribuire alla riduzione delle emissioni", conclude da Silva.
Rigenerare è diverso da riusare
La definizione di rigenerazione è stata stabilita nel 2016 in collaborazione con diverse associazioni internazionali e la metodologia di ZF si basa su di essa.La rigenerazione è un processo industriale per elaborare i ricambi usati in modo che possano svolgere la stessa funzione di uno nuovo; hanno la stessa garanzia di uno nuovo e il 100% di tutti i prodotti rigenerati sono testati secondo gli standard OE.
I ricambi rigenerati si differenziano da quelli usati per il fatto che:
• hanno la stessa geometria di un ricambio nuovo
• tutte le singole parti sono state pulite
• i componenti usurati o danneggiati (guarnizioni, elementi di fissaggio, ecc.) sono stati sostituiti
• rappresentano lo stato più recente della produzione e del software
• sono stati completamente testati.
Anche il processo di produzione della rigenerazione deve soddisfare determinati criteri. Tutti i vecchi ricambi che sono stati restituiti (core) vengono completamente smontati e puliti. Le parti usurate vengono selezionate, i componenti utilizzabili vengono rilavorati utilizzando processi produttivi adeguati (fresatura, rettifica, levigatura, ecc.). Dopo l'assemblaggio, tutti i prodotti vengono testati utilizzando gli stessi metodi di misurazione e di prova di un ricambio nuovo.