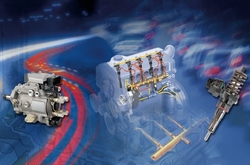
Ecologia, prestazioni e risparmio: sono questi gli spunti da cui la ricerca muove nell’ottimizzazione dei sistemi di iniezione. Vediamo cosa è cambiato, cosa cambierà e come prepararsi a un mercato in forte fibrillazione.
Isistemi di alimentazione del motore, insieme a quelli di sovralimentazione hanno subito, negli ultimi anni, alcune tra le più importanti evoluzioni tecnologiche. Motori più performanti ma anche più ecologici, hanno pesato sul mondo della distribuzione e dell’autoriparazione, costretta a specializzarsi e aggiornarsi continuamente. Analizziamo allora quali sono le principali novità del settore, comprese quelle date dal carburante alternativo che maggiormente è diffuso in Italia: il gas.Iniezione: il Common rail si candida a sistema universale
Partiamo dall’iniezione. Se nei motori a benzina si è forse raggiunta la soglia di migliorabilità, così non è nel settore del Diesel, sempre più protagonista del mercato. Pressioni sempre più elevate, nuovi meccanismi e un mercato in fermento: vediamo cosa sta cambiando e quali sono le prospettive di mercato.
Le novità del settore
Con attuatore piezoelettrico o con solenoide, poco importa il meccanismo che lo attiva, il sistema Common rail continua la sua ascesa come candidato unico a futuro sistema di alimentazione Diesel.
Il mercato del Diesel si sta espandendo, oggi oltre la metà delle autovetture vendute sono alimentate a gasolio e la ricerca sta movendo enormi passi nel miglioramento dei propulsori che utilizzano questo combustibile.
Bosch, Delphi e Denso: in ordine rigorosamente alfabetico, questi sono i principali competitor sul mercato europeo dell’Aftermarket. Se il primo marchio è storicamente il più presente come diffusione, e ancora leader nell’istallazione dei sistemi di primo impianto, gli altri non stanno a guardare. Denso e Delphi hanno da tempo capito che l’Europa è il faro di riferimento per ciò che riguarda l’innovazione nel settore automotive e stanno concentrando i loro investimenti per non perdere terreno. È a livello tecnologico che si gioca la partita, oggi solamente Bosch e Denso possono offrire degli iniettori con attuazione piezoelettrica, Delphi lancerà sul mercato la sua nuova linea con questo sistema nel corso dell’anno. Ma cosa cambia realmente? L’iniettore con attuazione piezoelettronica consente dei tempi di iniezione quasi istantanei e, grazie alle ridotte dimensioni del “nozzle”, ossia dell’ugello, anche una perfetta dosabilità delle quantità di carburante da iniettare. A fronte di ciò esistono però anche delle differenze basilari di progetto: mentre Bosch e Denso utilizzano un Common rail a flauto, la Delphi si distingue per la caratteristica forma a ragno. Ciò che è tuttavia evidente è come stiano aumentando le pressioni di esercizio: se oggi la massima è di circa 1.800bar entro l’anno si dovrebbero superare i 2.000bar, con evidenti vantaggi per il rendimento dei motori.
Anche la silenziosità è aumentata. Basti pensare che taluni sistemi di iniezione hanno una rumorosità di soli 3db(A) (la direttiva macchine, testo che regolamenta le caratteristiche tecniche di ogni componente meccanico, fissa a 80db(A) la soglia massima). Con l’iniezione multipla poi è migliorata anche l’efficienza: l’iniettore, è il caso del Multijet della Fiat, effettua delle iniezioni di carburante prima e dopo quella principale, che rendono omogenea e completa la combustione.
Cosa cambia per distributori e autoriparatori
Questa migrazione del sistema di iniezione dal tradizionale concetto di Diesel a “bassa pressione” alle nuove e mirabolanti frontiere dei 2.000bar e oltre comporta e comporterà un radicale cambiamento del settore ricambistico e della riparazione in generale. I costruttori di tali sistemi insistono sulla necessità di pulizia all’interno degli ambienti di lavoro, poiché anche una microparticella che dovesse infiltrarsi all’interno di un iniettore, alle pressioni cui lavora, potrebbe danneggiarne irrimediabilmente il funzionamento. L’ambiente di lavoro delle officine è quindi solo il primo a doversi aggiornare. Oggi, alcuni produttori (Delphi in prima linea) richiedono alle loro officine autorizzate di realizzare una cosiddetta camera pulita, da utilizzare per tutte per le operazioni di attacco e distacco dal veicolo dei componenti ad alta pressione, in pratica tutto ciò che si trova a valle del filtro carburante. Ovviamente la prassi si fa ancora più restrittiva nel caso di revisione di componenti quali la pompa ad alta pressione, il Common rail o anche il singolo iniettore: in questi casi è necessario essere dotati di un Clean Cabinet, ossia una postazione di lavoro pressurizzata a elevata pulizia. Gli standard sono quindi alti e viene spontaneo chiedersi se abbia senso parlare di revisione. Questi sistemi sono sempre più complessi, al punto che oggi solo pochissime officine possono permettersi il lusso di revisionare un iniettore. Il mercato, come in molti altri settori, sta mutando verso una dimensione orientata al consumo e questi componenti sono destinati al solo ricambio. Acquistare un banco prova iniettori Diesel è un investimento notevole di capitale, ma averne uno è importante per rilevare un eventuale danno e se necessario ordinare il ricambio.
Le nuove frontiere del mercato
Cerchiamo allora di capire quali sono le possibilità di questo nuovo mercato che si sta aprendo. Oltre il 50% delle autovetture immatricolate in Italia in un anno sono oggi Diesel. Bisogna poi tener conto del fatto che l’innovazione tecnologica porta a un sempre minore numero di guasti all’interno di una vettura, quindi, anche considerando una percentuale bassa, rimane il fatto che da qui ai prossimi dieci anni almeno la richiesta di iniettori di alta pressione come parti di ricambio resterà elevata.
Ma non solo per meccanici e distributori è cambiato il modo di lavorare. Abbiamo chiesto alla BCD Corona, una delle più importanti aziende italiane produttrici di pompe di alimentazione carburante, cosa sia cambiato nella loro attività con questi nuovi sistemi. Il risultato è che anche alla normale pompa a membrana, che “spinge” il gasolio dal serbatoio alla pompa di alta pressione, viene richiesta una potenza idraulica maggiore. Così nasce la pompa a pistone compatta, dieci volte più potente della equivalente a membrana, ma dello stesso ingombro.
Abbiamo parlato tanto di Diesel, perché è in questo settore che la ricerca sta maggiormente investendo negli ultimi anni e perché riteniamo che il trend non sia destinato a calare. Il mercato del ricambio per i sistemi di iniezione dovrà tenere conto di questo cambiamento e adeguarsi, come già fecero in passato le più grandi aziende produttrici di carburatori, i carburatoristi e tutto l’indotto di un sistema di alimentazione che oggi pare distante anni luce.
Turbo che passione - Compressori senza turbo? Non hanno futuro
Quando da un motore si desidera avere una potenza unitaria maggiore, il sistema più efficace è ricorrere a un compressore. Comprimendo l’aria di ingresso ai cilindri si riesce, infatti, a far affluire anche una maggiore quantità di carburante e quindi a migliorare le prestazioni generali del propulsore a parità di cilindrata. Non solo, nei motori Diesel il rapporto aria carburante non è fisso, come in quelli a benzina, quindi più aria entra, migliore è la combustione e conseguentemente sono minori gli sprechi di gasolio. La sovralimentazione nelle autovetture ha però sempre avuto un grosso limite, superato solo negli ultimi anni: il compressore, come tutte le macchine che in gergo tecnico sono definite a fluido, è progettato per dare la massima efficienza a un prestabilito numero di giri. Occorre a questo punto chiarire in quale maniera viene attivato il compressore. Esistono sostanzialmente tre modi possibili, che si riducono a due nelle applicazioni pratiche attualmente montate sulle auto: tramite un motore elettrico, attraverso una cinghia e collegandolo direttamente al motore, oppure calettando sul suo asse una turbina che “ruba” potenza ai gas di scarico. Teoricamente il primo sistema, con motore elettrico, sarebbe il più versatile, poiché consente una regolazione della velocità di rotazione indipendentemente dal quella del motore, ma finora non ha riscosso alcun successo: azionare il motore elettrico richiede infatti un grosso quantitativo di energia elettrica, che manderebbe in crisi la batteria. Anche il compressore attivato meccanicamente è in una fase di declino. Questo meccanismo di sovralimentazione ha infatti un grosso limite di rendimento: se è vero che viene utilizzato un compressore volumetrico, in grado di dare una pressione pressoché costante indipendentemente dal numero di giri, è anche vero che la potenza sottratta al motore per farlo muovere non è trascurabile. Il risultato è che il rendimento generale di questo sistema è relativamente basso e anche i costruttori più fedeli al “Compressor”, come la Mercedes, lo stanno lentamente abbandonando.
La sovralimentazione cambia stadio e il turbo si sdoppia
Per esclusione si comprende infine quale sia il sistema di sovralimentazione più in auge e su cui maggiormente si concentra la ricerca: il turbocompressore. Storicamente il problema di questo tipo di macchina era che, al di sotto di un certo numero di giri la turbina non operava in maniera ottimale e non riusciva a dare la giusta pressione al compressore. La soluzione si otteneva attraverso una valvola Waste gate di by-pass della turbina: appena la velocità dei gas di scarico era sufficiente, si chiudeva e chi guidava poteva avvertire una “spinta” aggiuntiva.
Negli anni Novanta, per ovviare il ritardo della risposta (turbo lag), è stato preso in prestito un concetto già presente nell’industria e che, si è pensato, potesse funzionare anche sulle autovetture: il VTG (Variable Turbine Geometry). Grazie all’adozione della geometria variabile si è quindi riusciti a rendere efficiente il turbocompressore anche ai bassi regimi. Non solo, il crescente peso dei motori Diesel nel parco circolante ha ridato vigore a questa macchina (una “macchina” è per definizione un insieme di pezzi o di organi, di cui almeno uno mobile, collegati tra loro e capace di effettuare una trasformazione di energia), che oggi è presente su molte delle ultime autovetture equipaggiate con l’iniezione diretta Common rail. L’ultima evoluzione di turbocompressore è attualmente montata sulla BMW 535; si tratta, anche in questo caso, di un meccanismo già utilizzato nell’industria della produzione di energia: il multistadio. Facendo lavorare più turbine e più compressori in serie si può, infatti, aumentare la pressione finale, ma soprattutto, grazie a opportune valvole di by-pass, si può ottenere una regolazione perfetta della pressione a ogni regime di rotazione. A bassi regimi di rotazione si attiva solamente la turbina di alta pressione (più piccola e più vicina al motore), che è calettata sullo stesso albero del compressore di bassa pressione. Come i giri del motore aumentano il sistema di valvole fa sì che parte dei gasi di scarico in uscita dalla turbina di alta pressione vadano a interessare quella di bassa pressione e attivino quindi il compressore di alta pressione, in questo modo si riesce a ottenere le pressioni desiderate in ogni momento. Inoltre, l’utilizzo di valvole nella regolazione dei flussi rende molto morbida la transizione dei fluidi sulle due turbine, rendendola non percepibile al guidatore.
Il cambiamento coinvolge tutti
Questi cambiamenti stanno lentamente investendo tutta la filiera dell’Aftermarket; assodato che per i produttori i cambiamenti sono notevoli, ma riguardano sostanzialmente l’ambito della ricerca e sviluppo, vediamo cosa cambia per distributori e autoriparatori.
La sempre maggiore complessità di questi sistemi ha l’effetto di vedere sempre più ristretti i margini per la rigenerazione dei turbocompressori, settore su cui molte officine hanno fondato una professione. I turbo a geometria variabile, per non parlare di quelli multistadio, sono infatti interfacciati con la centralina del motore e un’ampia parte di elettronica si è quindi interposta nelle sole operazioni meccaniche. Tuttavia non è questo il grande problema della revisione dei sistemi di sovralimentazione. Oggi è ancora possibile per un meccanico rigenerare una turbina, ma i costi sono elevati: oltre a uno strumento di autodiagnostica serve anche un banco equilibratore di buona qualità, perché le tolleranze di montaggio sono diventate molto più restrittive negli anni. Di contro, sono drasticamente diminuiti i prezzi dei sistemi completi di ricambio. Le stesse aziende produttrici, ma anche distributrici, recuperano turbine danneggiate ed effettuano una revisione a regola d’arte, così da poter reimmettere sul mercato prodotti come nuovi a prezzi concorrenziali; alcune aziende forniscono addirittura il ricambio rigenerato prima della riconsegna di quello danneggiato, dando all’autoriparatore la possibilità di non fare aspettare il proprio cliente e di tenere l’officina sgombra da una vettura smontata in attesa.
Il singolo pezzo? Sul veicolo industriale
La riparazione quindi è destinata lentamente a trasferirsi esclusivamente sui veicoli industriali. Il turbocompressore di una motrice ha dei costi non indifferenti (anche superiori ai 2.000 euro) e la sostituzione richiede comunque una notevole specializzazione. Il sistema di regolazione della geometria variabile, ad esempio, è azionato dall’impianto di aria compressa, che a sua volta viene regolato dalla centralina. Anche in questo caso quindi saranno solo poche officine specializzate a poter operare e la tendenza non dà segni di cambiamento nei prossimi anni.
Con il gas a tutta manetta - L’ecologia, i costi e uno scomodo concorrente
Chi invece sembra avere un futuro roseo è un sistema da anni bistrattato dall’automobilista medio: il gas. Complici i continui blocchi del traffico dovuti all’inquinamento atmosferico e i continui rincari dei carburanti tradizionali alla pompa, il gas sia esso metano o Gpl (Gas di petrolio liquefatto) ha destato l’attenzione di case auto e acquirenti. Al punto che oggi, come è stato fatto presente durante l’ultima edizione del Dealer Day, sempre più clienti entrano nei concessionari chiedendo autovetture Bi-fuel.
Interessante vedere però che, ad eccezione di pochissime Case, che comunque si rivolgono a installatori indipendenti per il primo equipaggiamento, gli impianti a gas sono tutti realizzati in retrofit. In questo settore l’Italia può dire ancora la sua, non solo come numero di installatori e punti di distribuzione di carburanti alternativi, ma anche come tecnologie.
Anche il gas ha il suo Common rail
Agli italiani il gas non è mai piaciuto per un semplice motivo, che è stato per anni nascosto da presunti rischi per la sicurezza e scarsa presenza di punti di distribuzione: la perdita delle prestazioni del motore. Siamo un popolo di guidatori, nessuno rinuncerebbe ad avere una vettura performante, anche se in autostrada non si possono superare i 130km/h.
Oggi però non è più così; i moderni motori omologati Euro4, a iniezione e con sonda Lambda, hanno richiesto un notevole sforzo ai produttori di impianti per adattare l’alimentazione gassosa a queste vetture. È nata così l’iniezione fasata, un sistema innovativo, che ha consentito agli impianti di migliorare notevolmente performance e sicurezza. Il sistema prevede l’istallazione di nuovi iniettori direttamente sul collettore di aspirazione in prossimità delle valvole. L’iniezione è realizzata tramite un meccanismo del tipo Common rail (esattamente come quello dei motori Diesel), con elettroiniettori comandati elettronicamente. Una centralina comunica in “real time” con quella della autovettura, seguendone istantaneamente i comandi di iniezione. In questo modo sono state eliminate tutte le possibili perdite nell’aspirazione e anche ogni rischio di “ritorno di fiamma”.
Il mercato della bombola
I numeri parlano chiaro: nel 2003, ultimo dato censito dall’ACI, il 3,95% dei veicoli era alimentato a gas. Ciò vuol dire che in Italia circolavano ben 1.355.630 autovetture con la “famigerata” bombola nel portabagagli. Nell’ultimo anno, anche se i dati non sono ancora stati pubblicati, si è registrato un lieve aumento delle iscrizioni di veicoli ibridi e per il prossimo, vista anche la massiccia campagna pubblicitaria fatta da più di una casa auto, la crescita dovrebbe proseguire, nonostante il possibile termine degli incentivi. Queste autovetture, volenti o nolenti, entreranno comunque nel circuito della riparazione, sia ordinaria, sia straordinaria ed è impossibile non tenerne conto. Ma c’è un problema…
E per la garanzia? Il caos
Quando un’auto con impianto a gas entra in officina per un intervento di manutenzione, esistono almeno quattro diverse possibilità: che il cliente abbia comprato un auto nuova Bi-fuel, ossia con impianto montato da o per conto della Casa; che la vettura sia stata equipaggiata con l’impianto a gas da o per conto del concessionario; che il veicolo sia ancora in garanzia, ma l’installazione sia stata effettuata dopo l’acquisto; l’auto è vecchia e ha l’impianto a gas. Nell’ultimo caso non c’è ovviamente alcun problema: ogni tipo di intervento che non coinvolga l’impianto di alimentazione alternativo (che è coperto dall’installatore) è a carico del cliente. Anche nel primo caso, ossia se l’autovettura è nuova e l’impianto è fornito in primo equipaggiamento, non vi sono dubbi: la Casa deve fornire la normale garanzia e ottemperare agli obblighi imposti dalle normative vigenti.
La faccenda si complica notevolmente, invece, nel caso in cui l’istallazione sia avvenuta dopo l’acquisto, sia che l’abbia fatta il cliente sia la concessionaria.
Analizziamo distintamente i due casi e cerchiamo di fare un po’ di chiarezza.
Se l’auto è stata acquistata e l’installazione effettuata dal proprietario, le Case hanno il diritto di non riconoscere la garanzia. Alcune di esse però limitano tale esenzione ai soli componenti coinvolti nella trasformazione, mentre altre lasciano invariata la garanzia su tutto il veicolo se l’installazione è stata effettuata da un partner della Casa stessa. Ancora più complessa la situazione degli impianti fatti installare dai concessionari. In questo caso è il singolo dealer che può offrire delle forme di garanzia sul veicolo, posto che la Casa non la preveda, quindi fa fede il contratto di vendita rilasciato al proprietario della vettura.
Per farla breve è impossibile, quando un’auto alimentata a gas entra in officina, sapere se è o non è coperta da garanzia, a meno che non sia scaduta, oppure che la vettura non nasca già con l’installazione in primo equipaggiamento.