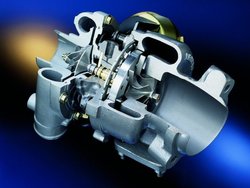
Pregi e difetti del turbocompressore a gas di scarico; presentazione tecnica di una metodologia che ha permesso di incrementare sensibilmente la potenza specifica dei motori a combustione interna.
Il funzionamento di un motore a combustione interna, sia esso alimentato a gasolio o a benzina dipende, in termini prestazionali, da due fenomeni naturali che ne limitano fortemente il rendimento: la composizione dell’aria e la pressione atmosferica.Per quanto riguarda la composizione dell’aria, ciò che influisce sulle performance del motore è la quantità di ossigeno (in peso al 20% circa). Se si tiene conto poi che l’azoto, presente invece in grande quantità, non partecipa attivamente al fenomeno della combustione, si capisce immediatamente come ci sia uno spreco in volume all’interno della carica fresca immessa nel motore. Il combustibile per bruciare, infatti, necessita di ossigeno e di conseguenza, data la composizione atmosferica, per ogni 20 parti di ossigeno che vengono inviate in camera di combustione sono presenti più di 78 parti di azoto.
Il secondo grande problema che attanaglia il rendimento dei motori alternativi è proprio quello relativo alla differenza di pressione che si riesce a creare tra la camera di combustione e l’ambiente esterno. Ed è proprio in virtù di questa differenza di pressione che il propulsore aspira, dall’ambiente esterno, l’aria necessaria alla combustione. Essendo però la pressione atmosferica pari a circa 1 bar è evidente che, anche pensando di avere il vuoto all’interno del cilindro e di limitare a zero le perdite fluidodinamiche nei collettori di aspirazione, la massima differenza di pressione sfruttabile sarà proprio quel bar che caratterizza l’ambiente esterno. Se poi il motore si trovasse a operare ad alta quota le cose peggiorerebbero ulteriormente visto che, con l’aumentare dell’altitudine, la pressione atmosferica tende a diminuire.
Quest’ultimo limite è stato superato introducendo la tecnica della sovralimentazione; si tratta di una metodologia basata su un principio teoricamente molto semplice: introdurre forzatamente la carica fresca nel cilindro.
Con il termine sovralimentazione si indica un apposito sistema che, montato su un propulsore a combustione interna, permette a quest’ultimo di raggiungere un più elevato riempimento dei cilindri rispetto a ciò che normalmente accade per un propulsore aspirato.
Come già anticipato, l’immissione della carica fresca nel cilindro è garantita dalla differenza di pressione che nasce tra l’interno del cilindro stesso e l’ambiente esterno. Il motore aspirato per sua natura è vincolato a lavorare con una differenza di pressione che, nel caso ideale, può essere pari al massimo a 1 bar e cioè alla pressione atmosferica (tralasciamo volutamente le soluzioni che sfruttano le leggi dell’aerodinamica per ottenere leggeri effetti di sovralimentazione). Nel caso di un motore sovralimentato si può, al contrario, aumentare la differenza di pressione e di conseguenza la quantità di carica fresca all’interno del cilindro.
L’effetto di sovralimentazione può essere ottenuto con macchine volumetriche di diverso tipo: il turbocompressore azionato dai gas di scarico (ne vedremo più avanti il principio di funzionamento), il compressore azionato da un motore esterno e, infine, il compressore mosso direttamente dall’albero motore attraverso l’uso di particolari rinvii dentati o a cinghia. Sebbene quest’ultima soluzione sia ancora oggi adottata da alcuni costruttori (vedi ad esempio la Mini Cooper S) la stragrande maggioranza dei motori sovralimentati fa uso dell’ormai affermatissimo turbocompressore a gas di scarico.
Il principio di funzionamento di un turbocompressore azionato dai gas di scarico è concettualmente piuttosto semplice; i gas combusti che fuoriescono dal motore durante la fase di scarico investono le palette di una turbina centripeta che, tramite un alberino, trasferisce il moto alla girante del compressore. Quest’ultimo aspira l’aria dall’ambiente esterno e la invia al motore; ciò che rende vantaggioso il funzionamento di un circuito di sovralimentazione è proprio l’aumento di pressione della carica fresca in ingresso al motore. Dal punto di vista termofluidodinamico il compressore è una macchina che trasforma l’energia cinetica di un fluido (in questo caso l’aria) in energia di pressione; in altre parole la colonna d’aria in arrivo dal sistema di aspirazione giunge all’imbocco del compressore con una determinata velocità e con una pressione pari a quella atmosferica diminuita delle perdite fluidodinamiche. Il passaggio nel compressore ne provoca una diminuzione di velocità e un innalzamento di pressione. In questo modo viene definitivamente superato il limite a cui devono sottostare i motori aspirati; l’aumento della pressione sul lato di aspirazione del propulsore permette, infatti, di ottenere un sensibile incremento del rendimento volumetrico e quindi un miglior riempimento del cilindro.
Per quanto tutto questo possa sembrare estremamente semplice, in realtà l’accoppiamento del turbocompressore con il motore a combustione interna è un’operazione estremamente delicata; ciò dipende dal fatto che il motore alternativo e il turbocompressore sono macchine estremamente diverse tra loro. Il corretto dimensionamento delle giranti e delle chiocciole, di turbina e compressore, e un’accurata gestione elettronica del motore hanno permesso oggi di ottenere propulsori turbo estremamente pronti.
Uno dei difetti che maggiormente attanagliano i motori sovralimentati, infatti, è rappresentato proprio dal ritardo con cui si avverte la risposta del turbocompressore, fenomeno chiamato, in gergo, turbolag. In pratica nel momento in cui il pilota preme sul pedale dell’acceleratore, provocando l’apertura del corpo farfallato, il propulsore inizia a prendere giri; ciò provoca un aumento delle portate dei gas combusti che a loro volta mettono in azione la turbina. Quest’ultima, essendo vincolata rigidamente al compressore, permette un incremento della pressione di alimentazione dell’aria in ingresso (la girante del compressore ruota con la stessa velocità angolare della girante della turbina); in realtà prima che tutto questo meccanismo si inneschi nei modi dovuti passa un tempo ben determinato che molto spesso viene avvertito, da chi guida, come un temporaneo mancamento di prontezza del motore.
Il principio di funzionamento del turbocompressore porta con sé alcuni importanti problemi che è bene tenere sotto controllo; il primo, forse il più importante, è legato alla crescita della pressione di sovralimentazione. Se non si prevede un adeguato sistema di controllo il sistema raggiungerebbe situazioni di funzionamento molto critiche (pressioni troppo elevate) che metterebbero a dura prova la resistenza strutturale del motore portandolo in breve tempo a rottura.
Questo tipo di controllo è affidato generalmente alla valvola wastegate (ovviamente gestita da una centralina controllo motore) che al raggiungimento della pressione scelta (in fase di progetto) si apre permettendo ai gas combusti di by-passare la turbina. Così facendo non tutti i gas in uscita dal motore investiranno la girante della turbina ma fluiranno direttamente nel condotto di scarico e quindi nel tubo di scappamento della vettura.
I motori moderni sfruttano le capacità dell’elettronica per ottenere il cosiddetto effetto overboost; in pratica la valvola wastegate viene fatta aprire con un ritardo prefissato, permettendo alla pressione di crescere sensibilmente per qualche frazione di secondo. L’effetto che si ottiene è un incremento di coppia che, nei motori più spinti, si manifesta con forti accelerazioni dell’auto su strada.
Il secondo problema legato ai motori turbo è quello della detonazione; la crescita delle temperature e dei valori di pressione in camera di combustione provoca frequentemente l’accensione spontanea della miscela aria benzina. Per ovviare a questo genere di problema è necessario utilizzare benzine a elevato numero di ottano; questa soluzione però non è sufficiente a scongiurare il problema della detonazione e pertanto i motoristi equipaggiano i propulsori con i sensori di detonazione. Questi ultimi sono dei cristalli piezoelettrici che trasformano gli effetti delle vibrazioni del monoblocco in un segnale elettrico analizzato dalla centralina. Il controllo elettronico del motore provvederà, in presenza di incipiente detonazione, a posticipare l’accensione della carica facendo così diminuire drasticamente le temperature e le pressioni massime raggiunte nel ciclo. La prestazione del motore subirà un calo sensibile ma ciò andrà a beneficio della sua affidabilità.
Il turbocompressore è un componente sempre più diffuso sui motori attuali; sui motori a gasolio poi, grazie anche al principio con cui si esplica il ciclo Diesel, trova la sua migliore applicazione e i turbodiesel moderni ne sono una chiara conferma.
Sui motori alimentati a gasolio, infine, stanno trovando sempre maggiore applicazione i turbocompressori a geometria variabile; grazie alla possibilità di poter orientare la distribuzione del flusso dei gas che investe la girante della turbina, questi gruppi di sovralimentazione hanno praticamente permesso di annullare completamente il ritardo di risposta ed oggi un turbodiesel a iniezione diretta (tipo Common Rail) con turbina a geometria variabile è capace di raggiungere la sua coppia massima anche prima dei 2000 giri/min.