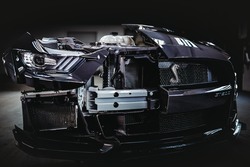
Come funziona il raffreddamento del veicolo? Quali sono i componenti fondamentali di questo sistema?
L’impiego della sovralimentazione e la ricerca della massima efficienza hanno elevato le richieste di controllo di tutti i parametri motore. In questo processo di ottimizzazione sono stati coinvolti anche i sistemi di raffreddamento.Quando uno studente del corso di ingegneria affronta l’esame di Fisica Tecnica, uno dei concetti fondamentali è che una macchina termica non potrà mai avere un rendimento superiore a quello di un ciclo di Carnot.
Senza entrare nel dettaglio matematico della questione, il ciclo di Carnot ci dice che il rendimento di una macchina termica cresce al crescere della differenza tra temperatura della sorgente fredda e temperatura della sorgente calda.
La sorgente fredda, in un motore a combustione interna, è quella a cui viene ceduta parte del calore prodotto dalla sorgente calda, ovvero l’ambiente esterno.
La sorgente calda è ovviamente il cuore del motore: cioè la camera di combustione, in cui avviene il processo di trasformazione dell’energia.
Tutto questo discorso giustifica l’importanza del sistema di raffreddamento di un motore, sistema che in questi ultimi anni si è evoluto in maniera importante, grazie anche alle possibilità offerte dai sistemi di controllo elettronico del motore.
I sistemi di raffreddamento moderni comprendono non solo il classico impianto con fluido refrigerante, ma anche quelli con intercooler per i motori sovralimentati e, nel caso di propulsori più spinti, i sistemi di raffreddamento dell’olio motore e di quello del cambio.
Ad acqua o ad aria?
Come sarà noto a molti, il raffreddamento del motore è necessario per svariati motivi. L’asportazione di calore dalle zone più calde, infatti, è fondamentale per evitare di sovraccariche termicamente le strutture dei componenti, ma anche per diminuire il rischio che si presentino fenomeni di detonazione dovuti a eccessivo riscaldamento.Il processo di raffreddamento deve essere poi attivato in modo uniforme, senza creare salti termici eccessivi, che potrebbero portare a deformazione delle singole parti.
I sistemi di raffreddamento impiegati in ambito automobilistico sono stati sempre di due tipi: ad acqua e ad aria. I due metodi indicati possono essere sviluppati, a loro volta, in due modalità differenti: nel caso di raffreddamento ad acqua, per esempio, ci sono gli impianti in cui la circolazione del fluido avviene per convezione (viene sfruttata la differenza di densità in funzione della temperatura, l’acqua calda si muove verso l’alto), appannaggio di motori molto vecchi, e quelli in cui invece la circolazione è forzata mediante pompa.
Se consideriamo il raffreddamento ad aria, invece, abbiamo che la ventilazione può essere indotta o dall’impatto dell’aria esterna sui componenti da raffreddare, oppure semplicemente utilizzando una ventola per ottenere quella che si chiama una ventilazione dinamica.
Tutto questo dal punto di vista strettamente teorico.
Nella pratica, la stragrande maggioranza dei veicoli oggi presenti sul mercato utilizza la circolazione forzata ad acqua (o meglio, una miscela di acqua e antigelo). Sempre per completezza di presentazione dell’argomento, possiamo ricordare che i sistemi ad aria vantano una grande semplicità costruttiva e un numero di componenti molto limitato.
È altresì vero che i sistemi a liquido offrono capacità di refrigerazione superiori.
Non solo: sempre in termini di confronto, i sistemi ad aria presentano ventole che assorbono parecchia potenza e il loro funzionamento è sempre abbastanza rumoroso.
Nei sistemi ad aria troviamo anche sollecitazioni termiche maggiori, che necessariamente richiedono di progettare accoppiamenti tra le parti con tolleranze superiori.
Come funziona il raffreddamento a liquido
Concentriamoci pertanto sui sistemi a liquido, di cui vale la pena ricordare il principio di funzionamento per linee del tutto generali.Quando un motore viene acceso, il circuito di raffreddamento è tarato per consentire un veloce raggiungimento delle condizioni di esercizio.
Per questo motivo, il flusso di liquido, durante i primi istanti di funzionamento, è diverso da quello che si osserva quando il motore è a regime.
Quando il motore è freddo, il refrigerante viene inviato al monoblocco e alla testa. Da qui, viene fatto ritornare alla pompa, da dove riparte con lo stesso giro fino a quando il termostato non verifichi il raggiungimento della temperatura di progetto che consente di passare all’utilizzo completo del circuito.
Una volta che il termostato si è aperto, il fluido refrigerante attraverserà anche il radiatore.
Concludiamo questo paragrafo ricordando che la quantità di volume di fluido refrigerante utilizzata si attesta mediamente intorno a sei volte il valore della cilindrata. Questo parametro, però, potrebbe cambiare a seconda delle tipologie di motore e di layout dell’impianto stesso.
I circuiti di raffreddamento a liquido, infine, lavorano a pressioni superiori a quella atmosferica, con valori compresi tra 1,5 bar e 2 bar. Questo è il motivo per cui alcuni motori funzionano a temperature anche prossime ai 100° C, senza che il liquido refrigerante raggiunga le condizioni di ebollizione.
Il radiatore
Fissato nella zona anteriore del veicolo, lo troviamo spesso accoppiato ad altri scambiatori di calore, tipicamente il condensatore dell’impianto di aria climatizzata e l’intercooler per il raffreddamento della carica compressa nei motori turbo.Il radiatore motore è certamente un componente cruciale dell’intero sistema. In camera di combustione si possono raggiungere temperature elevatissime, anche fino a 1.500° C e oltre. Il liquido di raffreddamento estrae il calore dal motore, raffreddando cilindri, valvole, testa, guarnizioni e molti altri componenti connessi.
Quello che però conta è sapere quali parametri tecnici possano inficiare il corretto funzionamento del radiatore. I residui lasciati dall’acqua e le impurità dovute ai depositi di antigelo scadenti, così come l’utilizzo di componenti turafalle, possono alterare, anche in modo considerevole, le prestazioni di un radiatore.
Talvolta, a creare problemi, è lo stesso termostato che, a causa di un suo malfunzionamento, può compromettere il corretto scambio termico a livello del radiatore.
Si tenga conto, poi, che la posizione di un radiatore è tale da renderlo uno degli oggetti più esposti a danni meccanici da impatto, dovuti all’urto contro pietrisco e insetti. Un radiatore che presenta anche delle piccole perdite, e che si trova a operare con un pacco radiante compromesso, potrebbe portare a un carico termico elevato ai danni di alcuni componenti fondamentali come testata e monoblocco. Con conseguenze facilmente immaginabili.
I radiatori moderni vengono realizzati solitamente in leghe di alluminio con luci tra le tubazioni variabili dai 10 mm ai 5 mm. All’aumentare della superficie radiante, ovviamente, aumentano le prestazioni del radiatore.
Gli intercooler per i sistemi di sovralimentazione
Il ruolo dell’intercooler, spesso noto anche con il nome di scambiatore aria/aria o, a seconda delle applicazioni, aria/acqua, è raffreddare l’aria in pressione inviata dal compressore sul lato di aspirazione del motore.Si tratta di aria compressa e quindi a temperatura elevata. L’abbattimento della temperatura consente di aumentarne la densità e quindi la quantità di ossigeno per unità di volume. Sotto il profilo operativo, i problemi tecnici provocati da un errato funzionamento dell’intercooler sono immediatamente riscontrabili attraverso la perdita sensibile di potenza del motore e un aumento del consumo di combustibile.
È importante sottolineare l’importanza di sostituire l’intercooler dopo la rottura del turbocompressore o in conseguenza a un suo malfunzionamento. I detriti e i residui di lubrificante carbonizzato provenienti dal compressore, infatti, intasano e danneggiano le sezioni di passaggio dello scambiatore.
I radiatori per il raffreddamento dell’olio
Il radiatore dell’olio motore è un componente che qualche decina di anni fa veniva montato principalmente su vetture ad alte prestazioni. Oggi è presente su molte auto.La presenza di questo componente rende ragione di una caratteristica a cui molti utenti spesso non prestano attenzione. L’olio motore, infatti, non ha il solo compito di lubrificare le parti in movimento relativo tra loro, ma assolve anche il ruolo di elemento raffreddante, aiutando ad asportare energia termica (calore) nelle zone più sollecitate di un propulsore. Per questo motivo, sono stati introdotti i radiatori per il raffreddamento del lubrificante, sia per la parte motore, sia per il comparto trasmissione.
Ancora più importanti sono i radiatori dell’olio pensati per i cambi automatici. In questo caso, si tratta di componenti progettati e sviluppati come gruppi totalmente autonomi e quindi posizionati talvolta in prossimità del cambio, talvolta nel comparto motore.
La sostituzione dell’olio motore a intervalli regolari è buona norma anche per preservare il funzionamento del radiatore dell’olio. Gli oli contaminati possono portare a ostruzione dei condotti del radiatore, riducendone le sezioni e limitandone di conseguenza il flusso con ovvie ricadute sulle prestazioni. Tornando invece ai cambi automatici, una delle cause più frequenti di rottura dei cambi stessi è proprio imputabile a un radiatore dell’olio compromesso.
Le ventole per il raffreddamento del radiatore
L’introduzione delle ventole elettriche è stato un passo importante nell’ambito della gestione termica dei motori.Un tempo, infatti, la ventola che forzava il passaggio di aria attraverso gli elementi radianti era direttamente collegata al motore. In occasione di traffico lento, o di soste prolungate in colonna, il basso numero di giri del motore si traduceva in velocità di rotazione basse per la ventola.
La ventola comandata da un motore elettrico ha permesso di superare questo enorme limite, assicurando non solo la possibilità di mettere in rotazione la ventola a una velocità indipendente da quella di rotazione del motore, ma, grazie alla gestione elettronica, è stato possibile decidere anche quando attivarla e quando fermarla.
Vale la pena considerare questo concetto come una delle maggiori conquiste del settore automobilistico moderno. L’adozione dell’attivazione mediante motori elettrici ha infatti permesso di ottenere risparmi energetici incredibili per numerosi utilizzatori.
Si pensi al servosterzo elettrico, alla pompa dell’acqua elettrica e a tutti quei sistemi che sono stati resi indipendenti dal funzionamento del motore e quindi attivabili solo quando necessario, un metodo intelligente per non sprecare energia.
Detto ciò, è ovvio che la ventola a comando elettrico è esposta alle tipiche avarie che interessano l’impianto elettrico. Un suo mancato funzionamento è causa di pericolosi surriscaldamenti del motore.
Un’ultima nota importante riguarda il senso di rotazione della ventola: durante il suo funzionamento, la ventola ruota in senso tale da richiamare aria dalla parte frontale del motore e inviare quella calda verso la parte posteriore del veicolo. In passato, capitava spesso che il collegamento elettrico della ventola, in occasione di una procedura di manutenzione, venisse invertito, provocando un’inversione del senso di rotazione della ventola stessa. In questo caso, l’operatività sarebbe totalmente compromessa, perché verrebbe aspirata aria calda dal motore che, a sua volta, sarebbe inviata al radiatore.
Le pompe nei sistemi a liquido
La pompa acqua, come anticipato, si occupa di mantenere la circolazione del liquido all’interno del circuito. Si tratta di un componente che, una volta guastato, non può essere riparato, ma deve essere sostituito.Spesso, la sostituzione della pompa dell’acqua avviene in occasione dell’intervento sulla cinghia di distribuzione, tanto che molti kit di sostituzione del comando della distribuzione prevedono già la pompa dell’acqua tra i componenti da rimpiazzare.
Le pompe acqua sono azionate o da cinghie Poly-V o da motori elettrici. Nel caso in cui si debba sostituire la sola cinghia Poly-V, è inutile installare una nuova pompa dell’acqua, a meno che questa non presenti danni evidenti. Tra le tecnologie maggiormente impiegate sulle pompe di ultima applicazione, possiamo ricordare i supporti integrali con cuscinetti a rulli o a sfere, per un funzionamento silenzioso e con basse perdite meccaniche per attrito, e l’utilizzo dei premistoppa in carbonio e carburo di silicio.